REFRESH
The REFRESH project – Smart, circular recycling of composite wind turbine blades
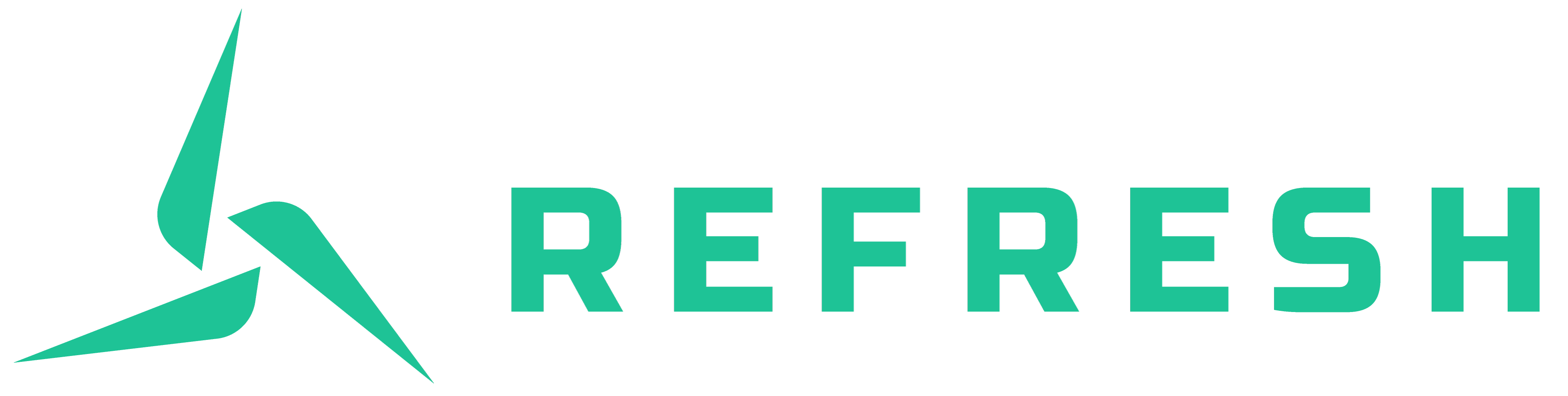
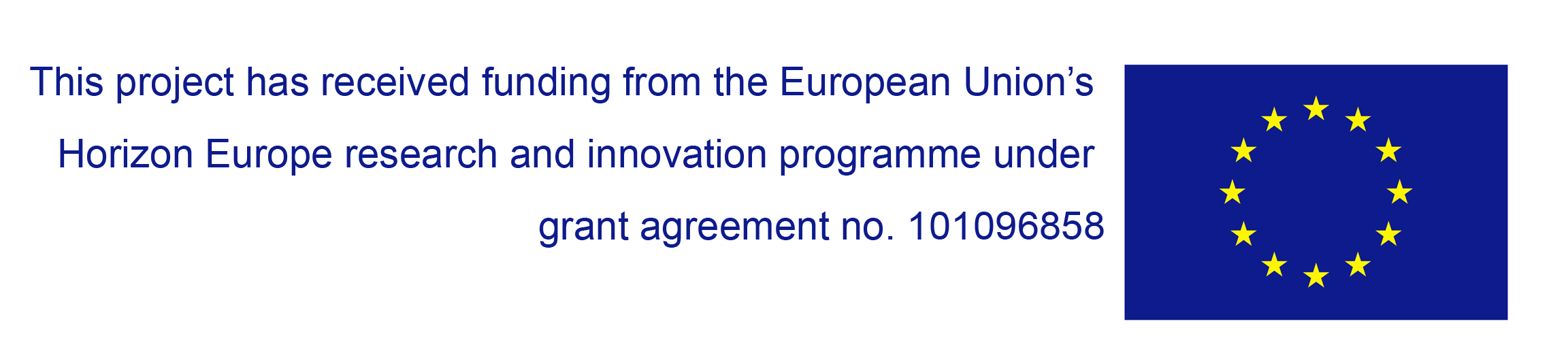
The REFRESH concept for building a circular and self-sustainable value chain foresees three steps. When a wind blade is decommissioned, the optimal recycling process will be selected according to the technical condition of that blade and current market demand. This will be achieved by using a dedicated tracing tool for collecting, protecting and sharing information and an embedded decision-making software for selecting the most sustainable approach to recycling at that time. The project will focus on the most robust and mature mechanical treatments, where composites are ground into particles which are used in the manufacture of panels for various markets, and thermo-chemical technologies (pyrolysis and solvolysis) which allow the recovery of fibers and synthetic oils. Other process and re-use options will also be investigated. A range of new products resulting from the outputs of the different processes will be designed. The approach developed within the project will be validated by means of life cycle assessment (LCA) and life cycle costing (LCC) analyses.
Project innovations include:
- Design of portable dismantling, shredding and sorting technologies
- Development and customization of recycling processes
- A new circular business model
- A novel digital blockchain traceability platform covering the whole supply chain
Building a new circular economy strategy for turbine blades will have a breakthrough impact in the wind energy sector. The REFRESH concept has significant potential for replication in other large and high-value markets where the use of composite materials is increasing (including aerospace, automotive, and marine).
REFRESH has received funding from the European Union’s Horizon Europe research and innovation program under grant agreement no. 101096858. The project commenced in January 2023 and will last 4 years.
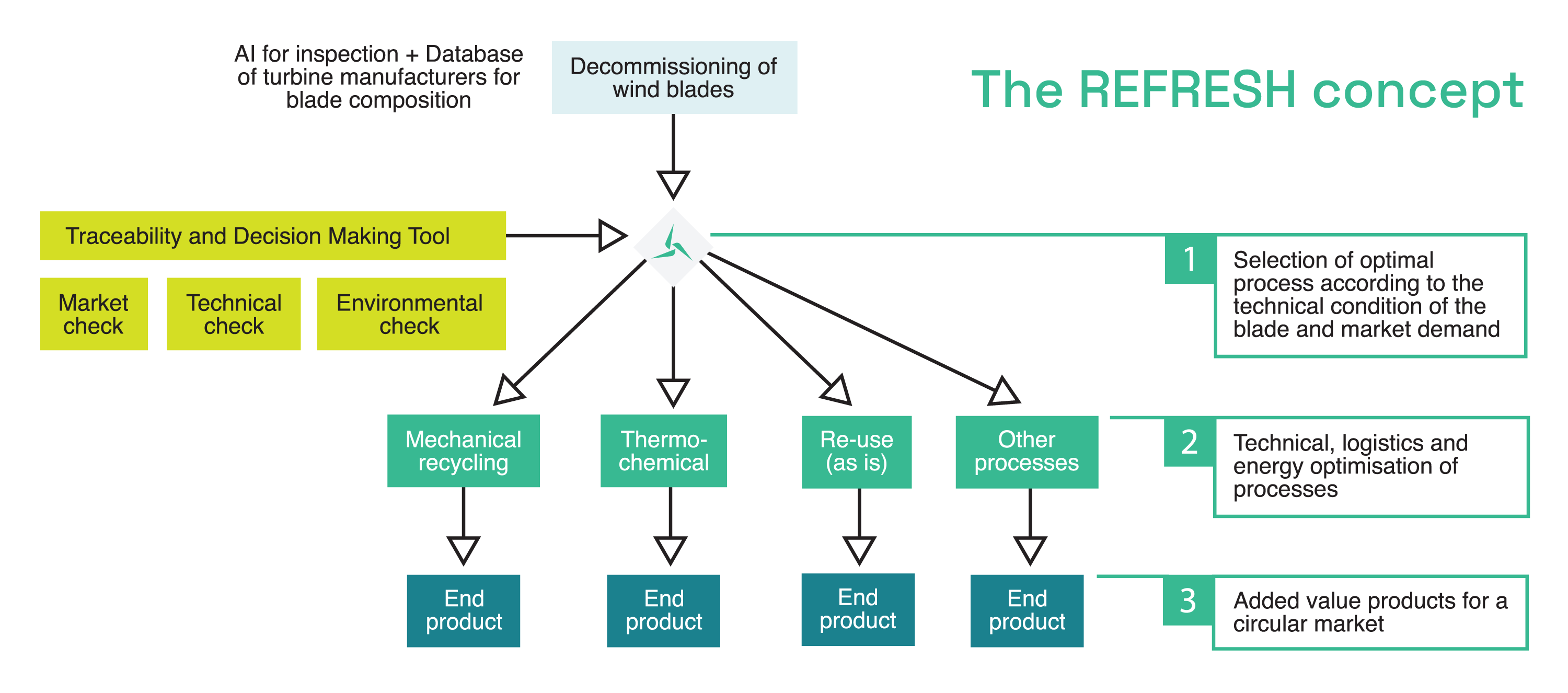
ENECOLAB is participating in Work Package 1: Design of portable dismantling, shredding and sorting technologies, which is developing technologies to cut and shred the turbine blades and sort the resulting materials for recycling. Using its thermo-chemical technology, ENECOLAB will convert the dust and fines produced during these processes (which are suitable for recycling) into energy and by-products.
Wind blades, sample 1
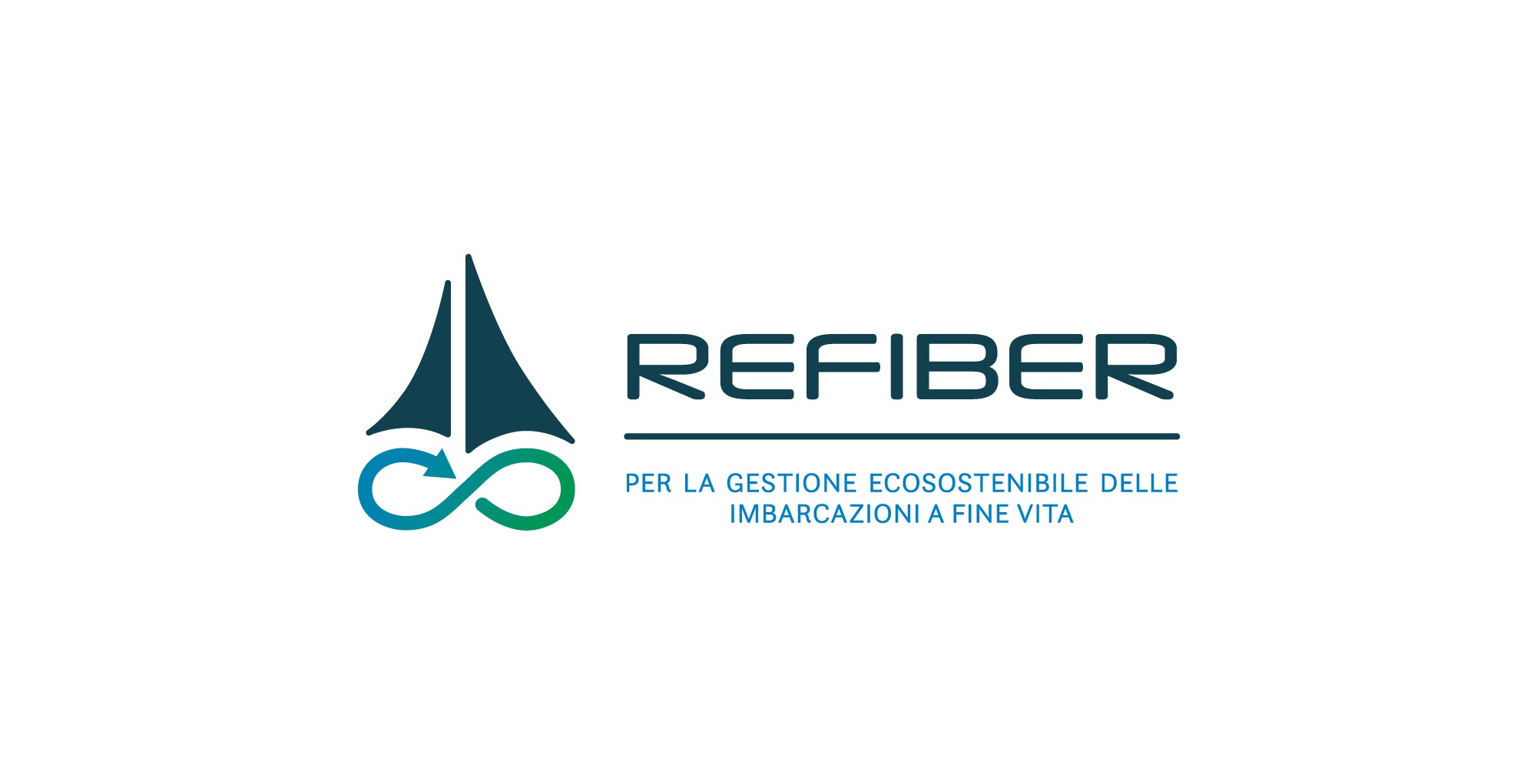
REFIBER
The REFIBER research program, developed by Area Science Park and Innovando Srl, studies the technical, economic and legal feasibility of a national system for the management of pleasure boats that have reached the end of their service life.
The program involves the study and adaptation of a regulatory framework based on the EPR-Extended Producer Responsibility scheme for manufacturers and distributors of pleasure boats, a policy already consolidated and used for other types of products (e.g. WEEE, batteries).
The absence of an organized regulatory and operational collection scheme for the recovery and treatment of hulls at the end of their life and the high costs of deconstruction and subsequent disposal of the materials that compose them, cause a major environmental problem: the abandonment of hulls on coasts. These abandonments damage the marine ecosystem for years. However, when boats are recovered, the most commonly used solution is the disposal of the fiberglass in landfill which, at 60% by weight, represents the most abundant and most difficult fraction to treat.
REFIBER therefore intends to contribute to the community objective of reducing waste sent to landfill and transform this problem into economic opportunities; supports the research and development of new technological solutions for the recycling of fiberglass, valorising the resulting secondary raw materials, in line with the principles of the circular economy, and overcoming regulatory barriers (lack of an End of waste decree on fiberglass).
Within this project, Enecolab’s mission is to find an economic and ecological solution to energetically enhance the organic portion of the fiberglass and to make the inorganic portion available for other industrial processes.